
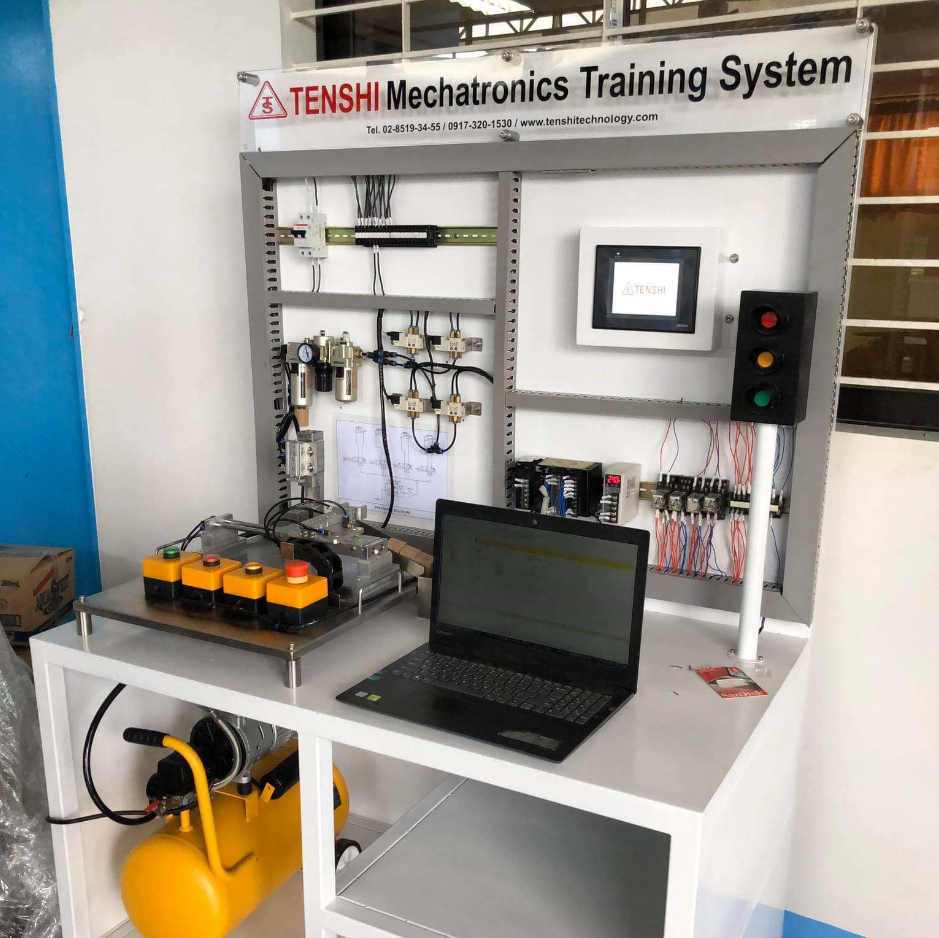
This workflow is supported by the identified abstractions of simulations for performing design-space exploration and for configuring Degrees of Freedom of the designed system.
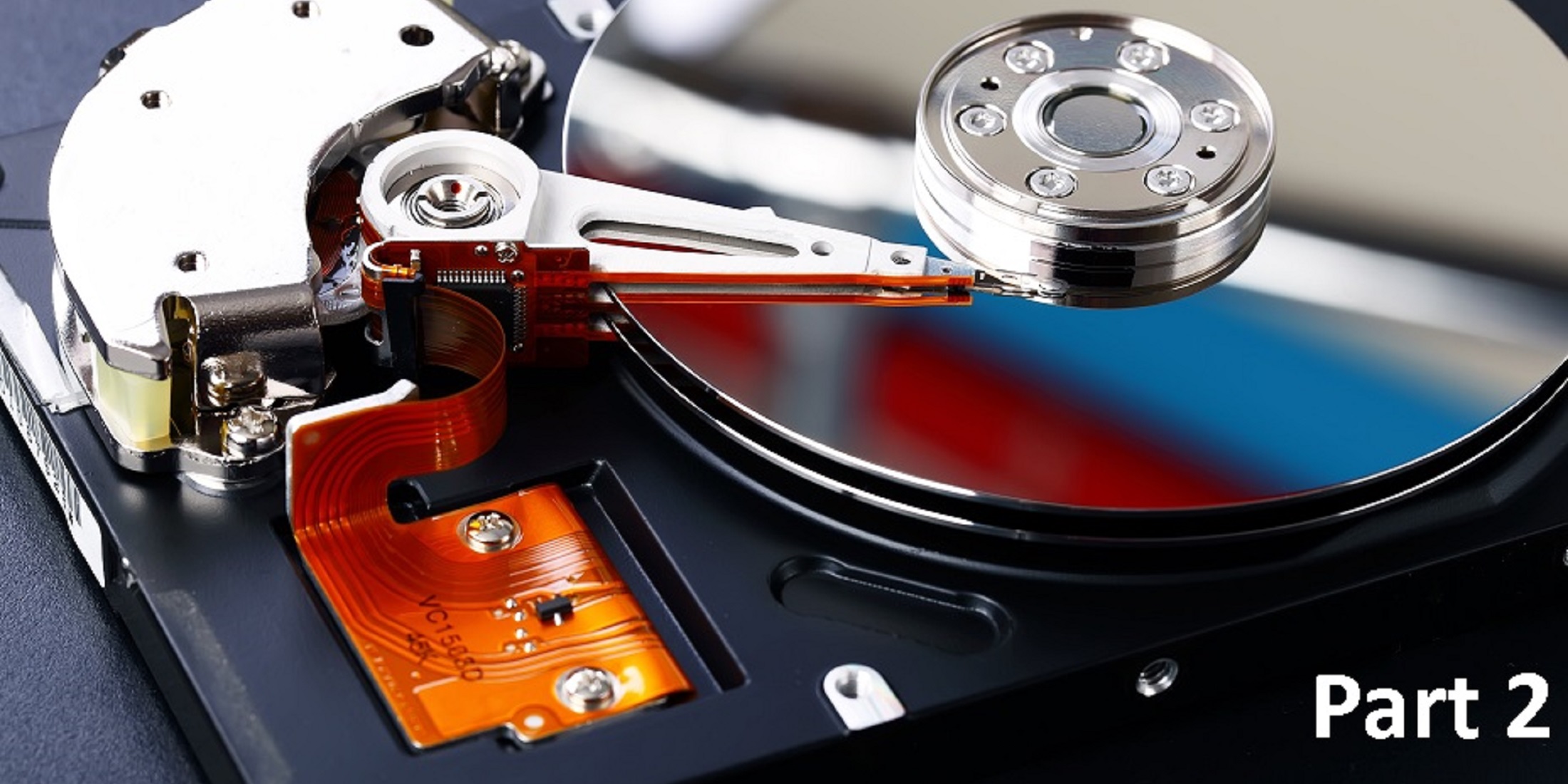
A design workflow for cyber-physical production systems is defined from stakeholder requirements to the final system. Throughout this work, Platform-based Design is refined and adopted to the design of cyber-physical production systems. Platform-based Design is selected: a design methodology introduced for embedded systems but currently utilized in different domains. In fact, tools must be utilized within a design methodology: a structured workflow of design activities. Eventually, modeling and simulation tools are not sufficient for designing systems. Power-Oriented Graphs energetic technique is utilized and adopted to the modeling of production systems. Energetic modeling techniques are consolidated approaches for modeling the dynamic of physical systems. Simulations provide valuable results as long as models able to predict the behavior of real systems are identified.
#System designer mechatronics software
Heterogeneous composition proposed within Ptolemy II software is utilized and adopted to production systems, in order to identify a picture of simulations available for their design. To evaluate the behavior of the system as a whole, these models must be composed so that their properties can be considered together. Each model typically represents only one aspect of the entire system, and thus only part of its total behavior. Integration of disciplines can be reached through models. To cope with the growing role of electronics and computer science, there is the need of concurrent design approaches which integrate physical and cyber design. Sequential approaches have been shown to be no longer efficient. For example, mechanical cams were replaced by cam profiles actuated through servomotors which are controlled from software deployed in real-time controllers. Mechanics based systems have shifted to cyber-physical production systems. Today, production systems are required more and more functionality and flexibility. Electronics and computer science played marginal roles filling needs and gaps of mechanics. The design of these systems was sequential and driven by mechanics. In this way, production systems were able to perform cyclic functionality. Few electrical motors drove cam shafts connected to physical tools. production lines and automatic machines of manufacturing industries) consisted of mainly mechanical components. Readers of this text will be equipped with all the tools necessary to plan, test, and implement a well-designed mechatronic system.Traditional production systems (i.e. A collection of case studies drawn from a variety of industries (complete with parts, lists, setup, and instructions) are used to support the authors' applied, design-oriented approach. The book features extensive coverage of the modeling and simulation of physical systems made possible by block-diagrams, the modified analogy approach to modeling, and state-of-the-art visual simulation software. Core aspects are combined with practical industrial applications and are presented in an optimal way for understanding. Students are introduced to all the topics needed to develop a good understanding of the basic principles used in mechatronics technology through the use of examples, problems and case studies, all of which can be quickly and affordably assembled and investigated in laboratory settings. This text by Shetty and Kolk, blends the pertinent aspects of mechatronics-system modeling, simulation, sensors, actuation, real-time computer interfacing, and control-into a single unified result suitable for use in the college-level mechatronic curriculum.
